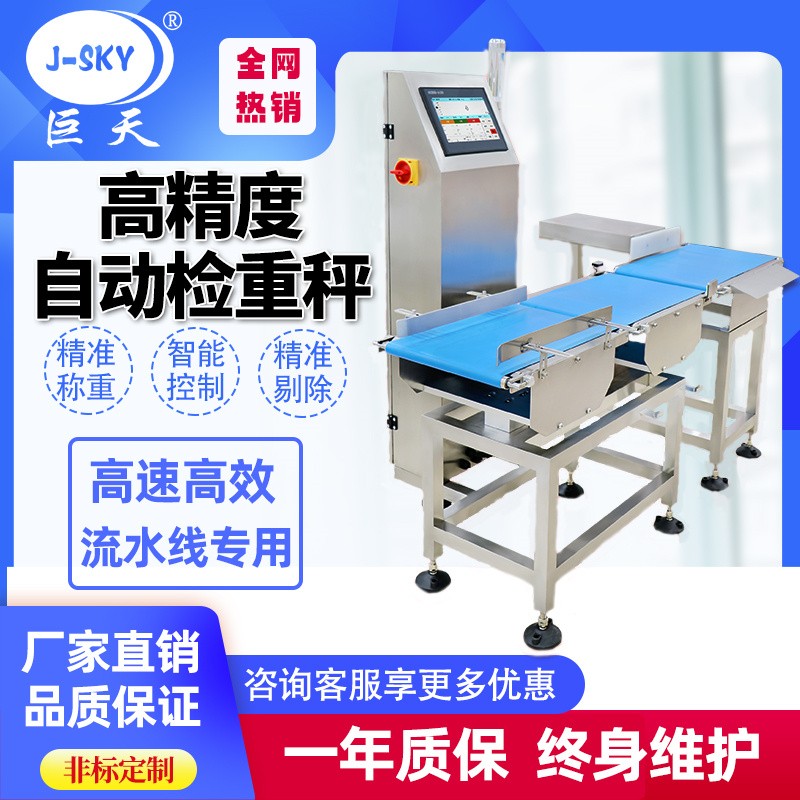

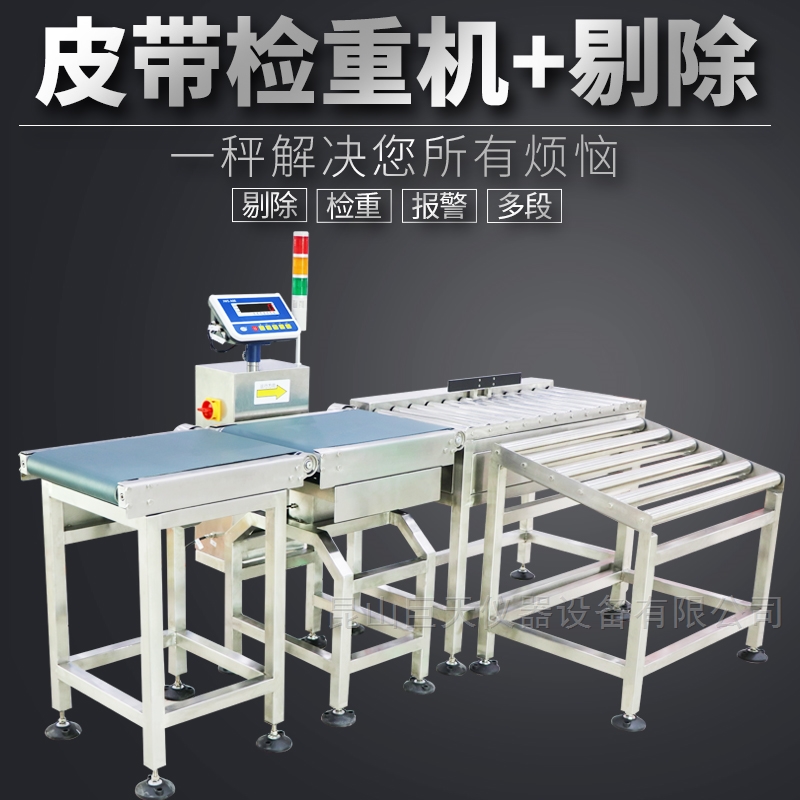
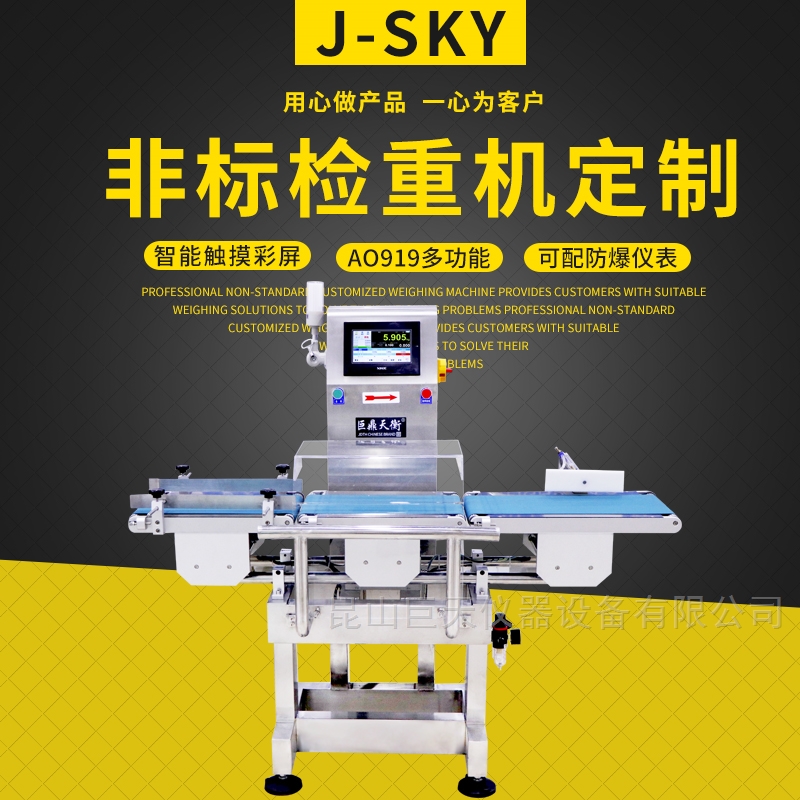
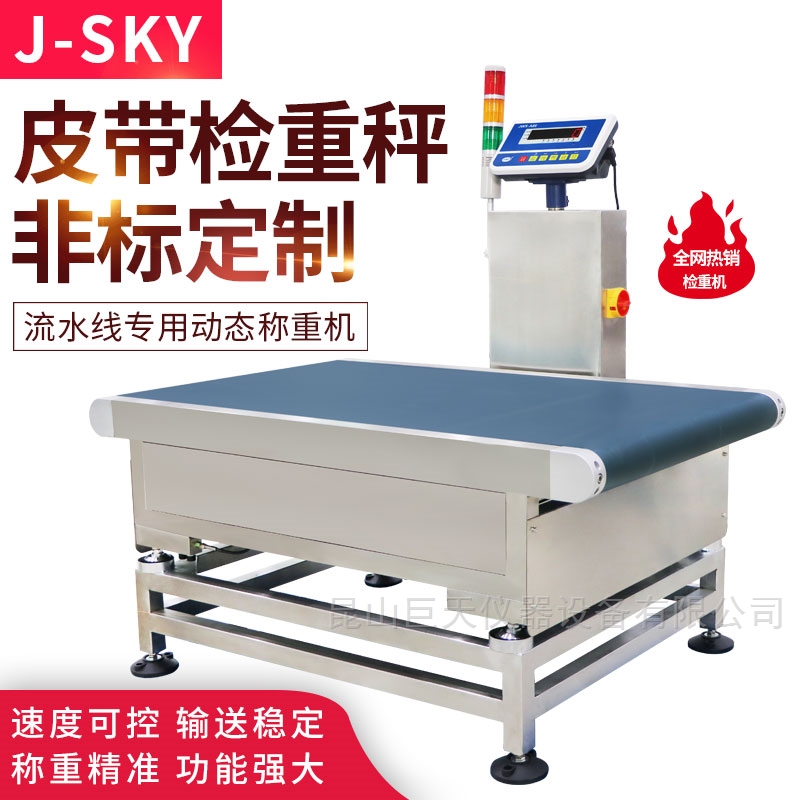
动态校准通过优化检重秤的实时反馈机制,显著减少生产中的原材料浪费,具体作用机制和效果如下:
一、精准控制灌装量
实时反馈调节
动态校准后的检重秤能实时监测产品重量,并将数据反馈给上游灌装设备(如灌装机、包装机),自动调整灌装参数。例如,当检测到产品重量连续偏轻或偏重时,系统会立即修正灌装量,避免因设备漂移导致的过量填充或欠重问题210。
误差范围最小化
动态校准可识别并修正因机械振动、温度变化引起的称重误差,将重量偏差控制在±0.05g至±0.5g范围内,减少单件产品的超重损耗。例如,在食品灌装场景中,每减少1g超重,年节省成本可达数万元47。
二、减少包材浪费
剔除不合格品
动态校准确保检重秤精准识别超重/欠重产品,并通过自动剔除装置(如气动推杆)移除缺陷品,避免包材(如瓶、袋、标签)因返工或报废产生的浪费19。
优化包装完整性
校准后的设备能检测包装内缺失件(如说明书、配件),避免因漏装导致整件产品报废,减少连带性原材料损失411。
三、数据驱动的生产优化
趋势分析与预警
动态校准过程中记录的重量分布数据,可生成生产趋势报表。例如,统计平均重量偏差后,优化灌装目标值,将平均超重率从1%降至0.3%,显著降低长期浪费714。
工艺参数调整
通过校准数据识别生产瓶颈(如灌装速度与称重精度的矛盾),调整设备参数或生产线布局,提升整体效率并减少调试期的原料试错成本816。
四、预防性维护降低损耗
设备状态监测
动态校准可检测传感器、传送带等部件的性能衰减,提前预警维护需求。例如,传感器灵敏度下降导致的重量误差增大,及时更换可避免批量产品超重报废619。
延长设备寿命
定期校准减少机械部件(如电机、轴承)因长期误差积累产生的异常磨损,降低维修频率和停机导致的原料浪费1718。
五、合规性保障与成本规避
避免法规处罚
动态校准确保产品净含量符合《定量包装商品计量监督管理办法》等法规要求,规避因重量不达标导致的罚款或召回损失13。
减少客户投诉
精准的重量控制提升客户对产品一致性的信任,降低因投诉产生的退货或补偿成本49。
应用案例
食品行业:某乳制品企业通过动态校准将酸奶灌装误差从±2g降至±0.5g,年节省原料成本超50万元7。
制药行业:药片包装线校准后,缺粒检测准确率提升至99.9%,减少包材浪费30%1。
通过以上机制,动态校准不仅直接降低单件产品浪费,还能通过数据优化和预防维护实现系统性成本控制。建议企业每月至少校准一次,并在生产线改造或原料特性变化时增加校准频次